Processes
1) Harvesting Kozo
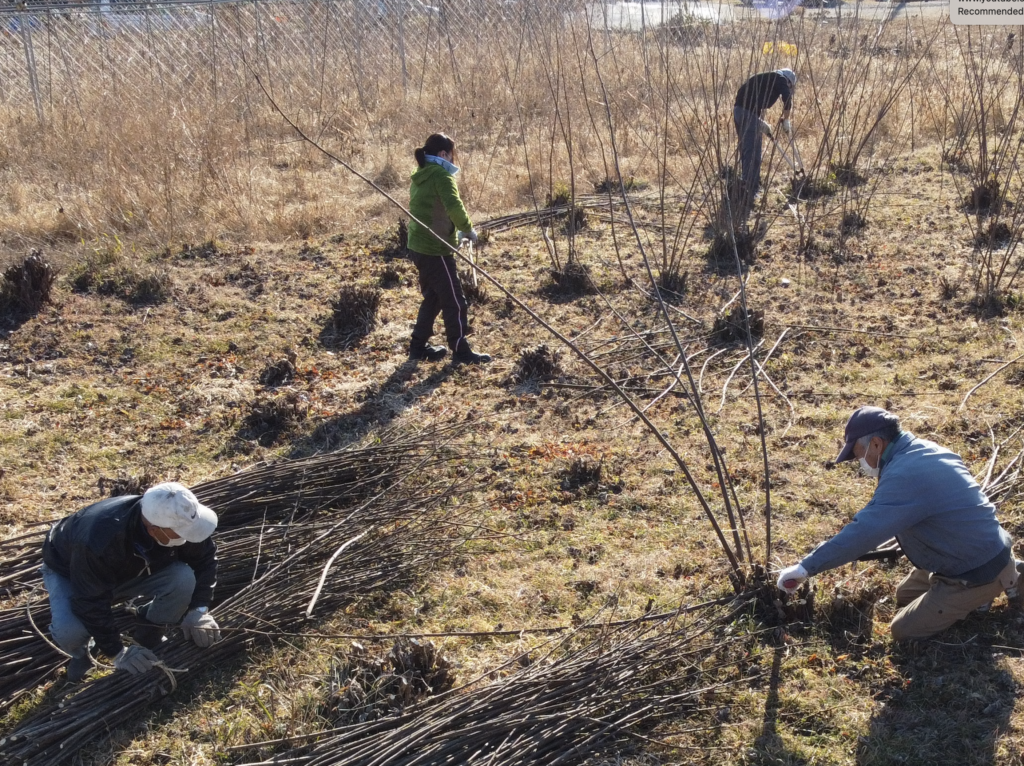
Hosokawa-shi is made from domestic osokawa-shi is made from domestic kozo which is a member of the mulberry family. It is harvested around January and February. Kozo is locally called “Kazu”.
2) Trimming Kozo
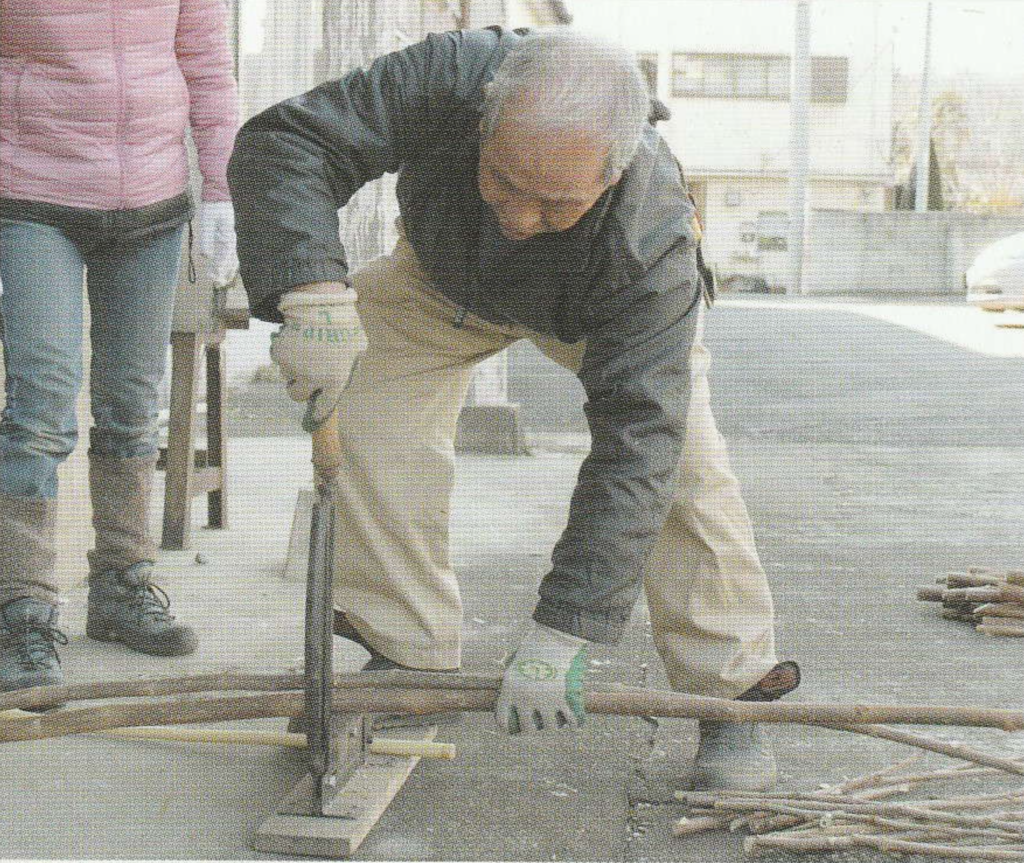
The harvested kozo shoots are cut to a lengtThe harvested Kozo shoots are cut to a length of about 70cm to 90cm.
3) Steaming the Shoots
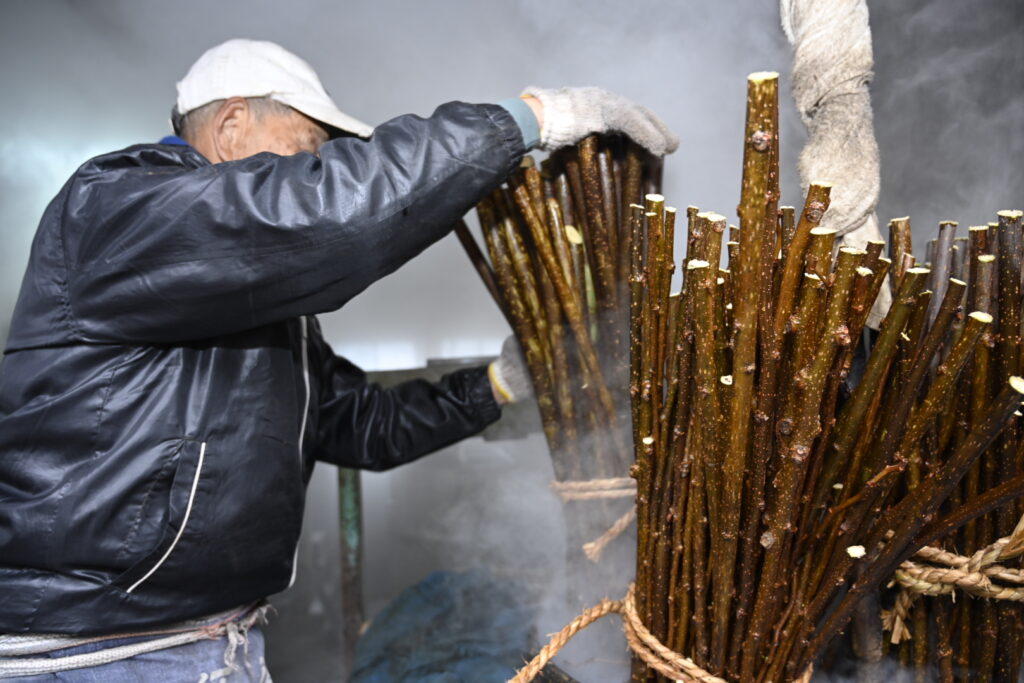
The kozo shoots are placed fat-end-The kozo shoots are placed root-side-down in a cauldron and steamed.
4) Stripping the Bark
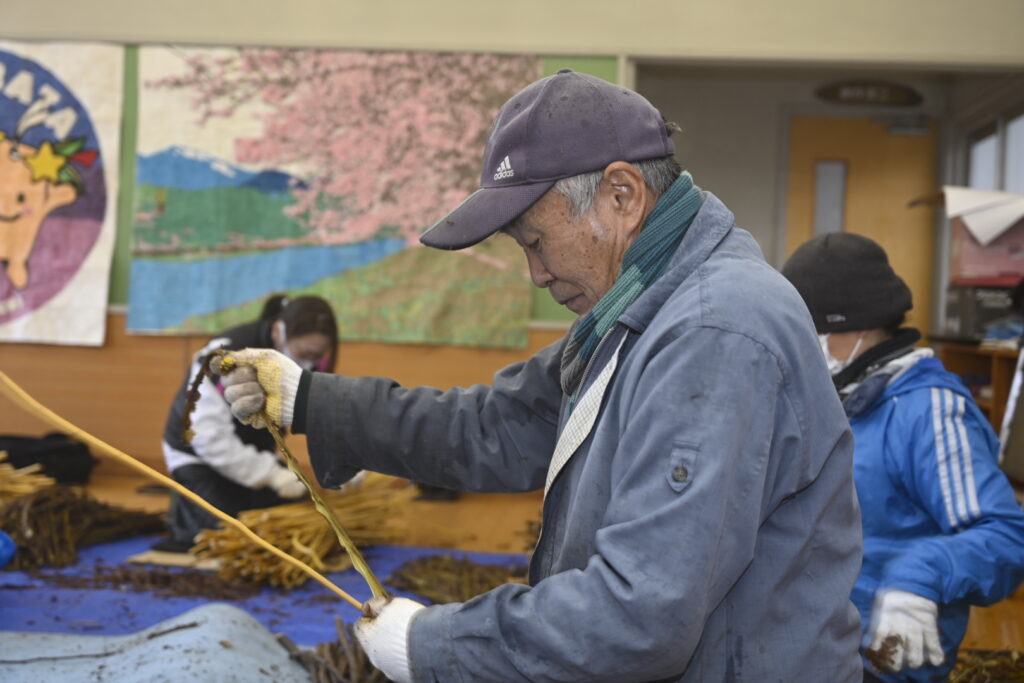
The bark is immediately peeled off right after steaming.
5) Scraping the Bark
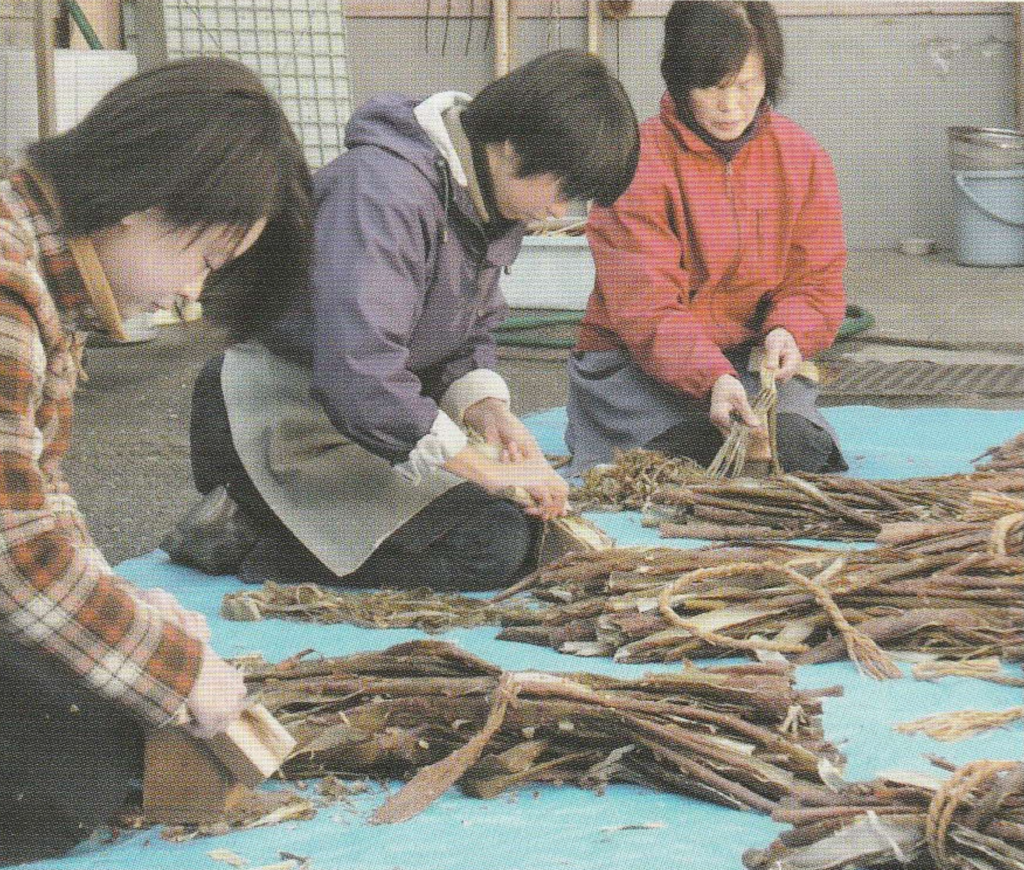
The dark outer layer of the bark is scraped off, leaving only the white bark within. The dark layers and any blemishes are carefully removed. This task is essential to the production of high-quality paper.
6) Boiling the Bark
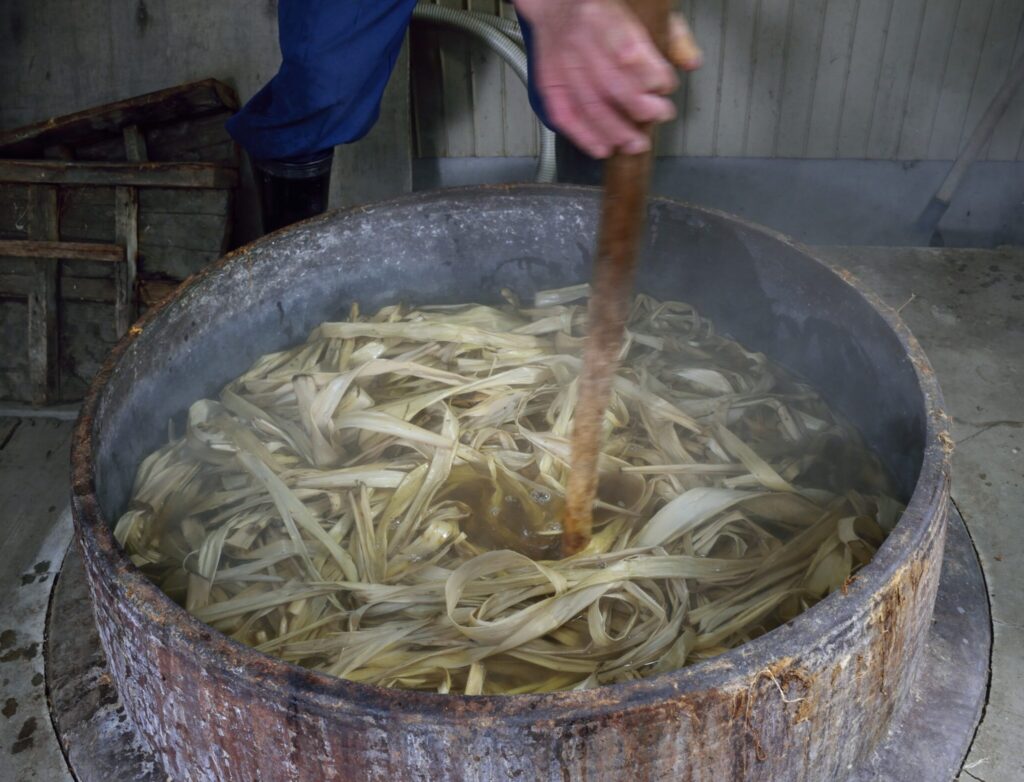
The prepared bark is boiled in a cauldron. When the water comes to a boil, soda ash (sodium bicarbonate) is added. It softens the white bark and removes impurities. The individual fibers are now easily separated.
7) Washing and bleaching
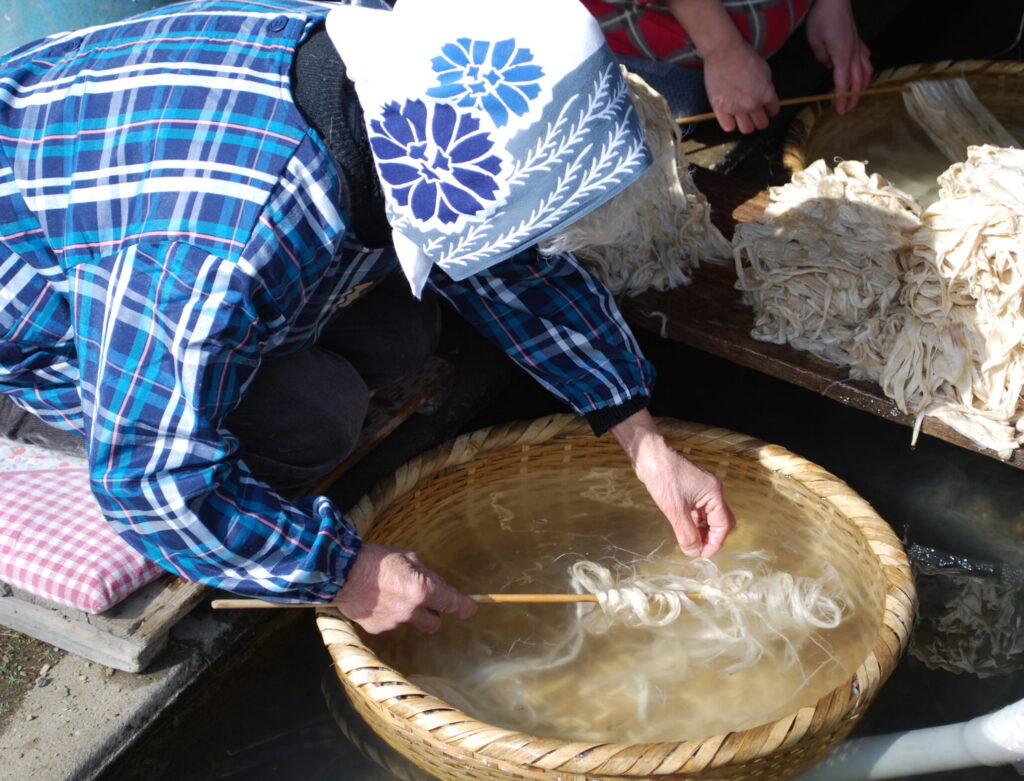
When the white bark has been completely cooked, it is placed in cold water where it iWhen the white bark has been completely cooked, it is placed in cold water where it is cleansed of any alkalinity and bleached by the sun. The white bark is then pulled out one by one with a bamboo stick and again, any residual matter and discoloration are carefully removed.
8) Pounding the Kozo
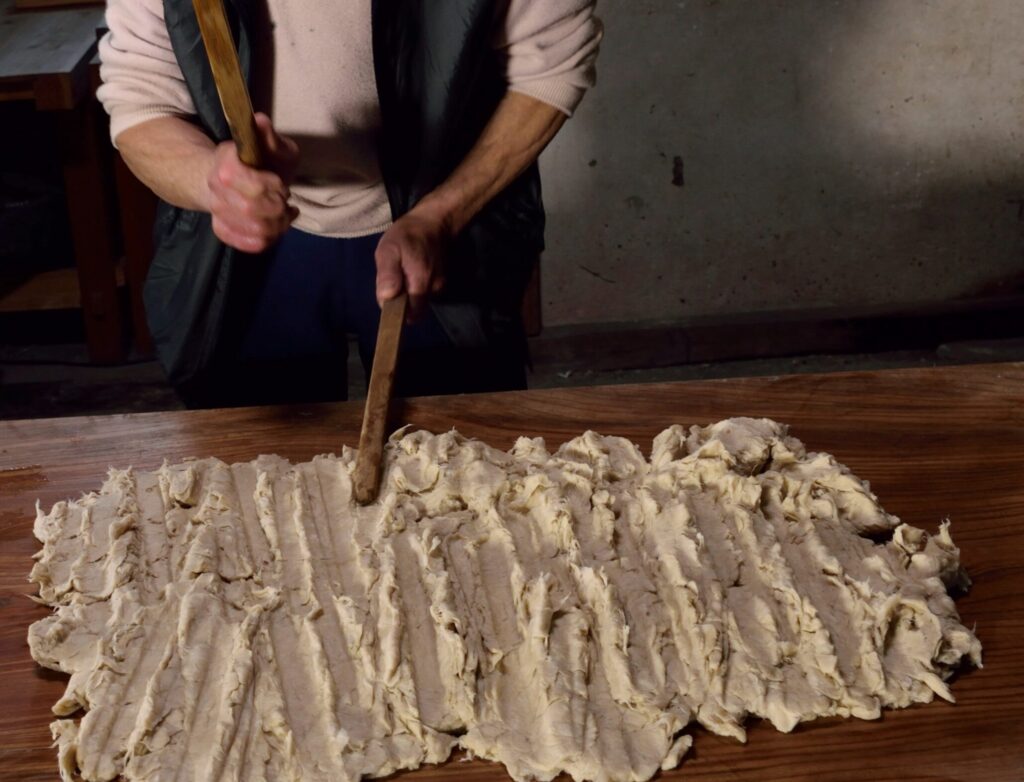
To further loosen its fibers in preparation for papermaking, the kozo is struck repeatedly with hardwood rods.
9) Striking the Tororo Aoi Roots

Another essential material when making paper is Neri. This mucilage, or viscous starch, is extracted by crushing the root of the tororo-aoi (Sunset hibiscus) plant. When placed in water, Neri acts as a suspending agent, spreading the fibers of kozo evenly throughout. In the paper making process, neri works to bind the fibers together. Since it is not sticky, the individual layers of paper can be pulled apart one by one during the drying process.
10) Making the paper

The combined materials (water, kozo, and neri) are put into a sukibune (paper making vat) and evenly mixed. Grasping the mold, the papermaker scoops up some of the mixture and pours it across a bamboo screen repeatedly, rocking the screen back and forth until the pulpy fibers have spread evenly over the surface. The washi sheets are moved to kanda (paper beds), onto which they are stacked one by one.
11) Drying
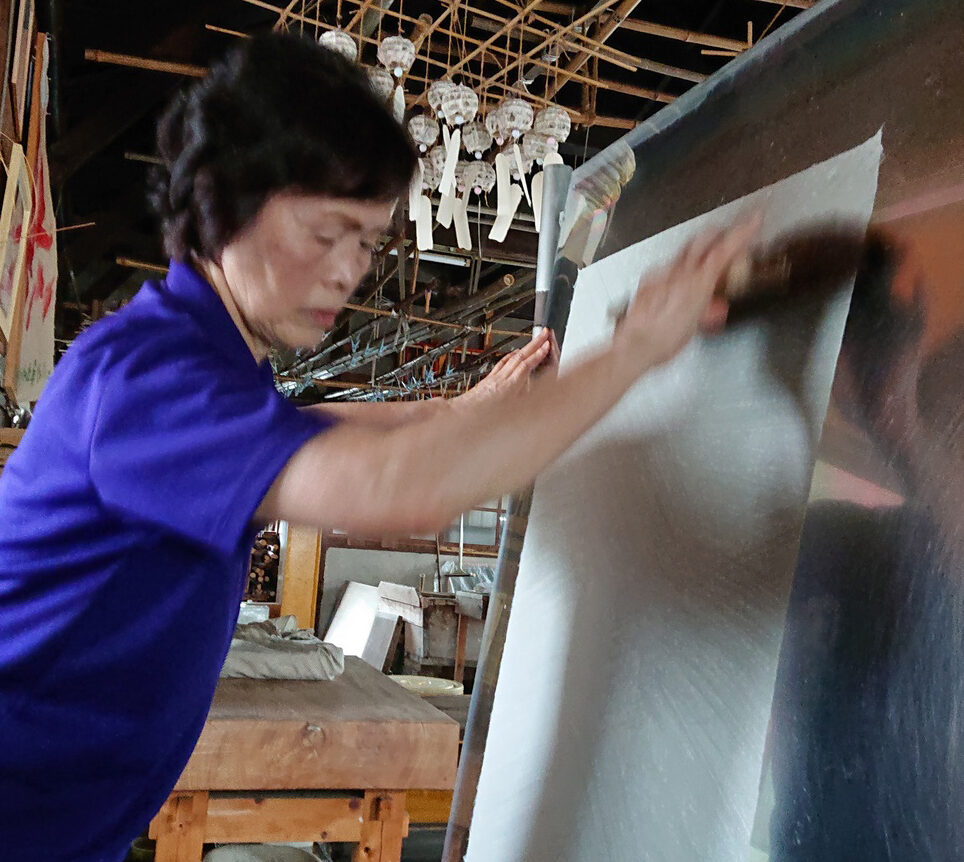
The pressed sheets are peeled off one at a time and placed on wooden boards to dry in the sun. When paper is placed on a board and dried in this way, it results in a unique wood grain pattern. These days, a heated iron plate is often used to dry the paper.
12) Sorting
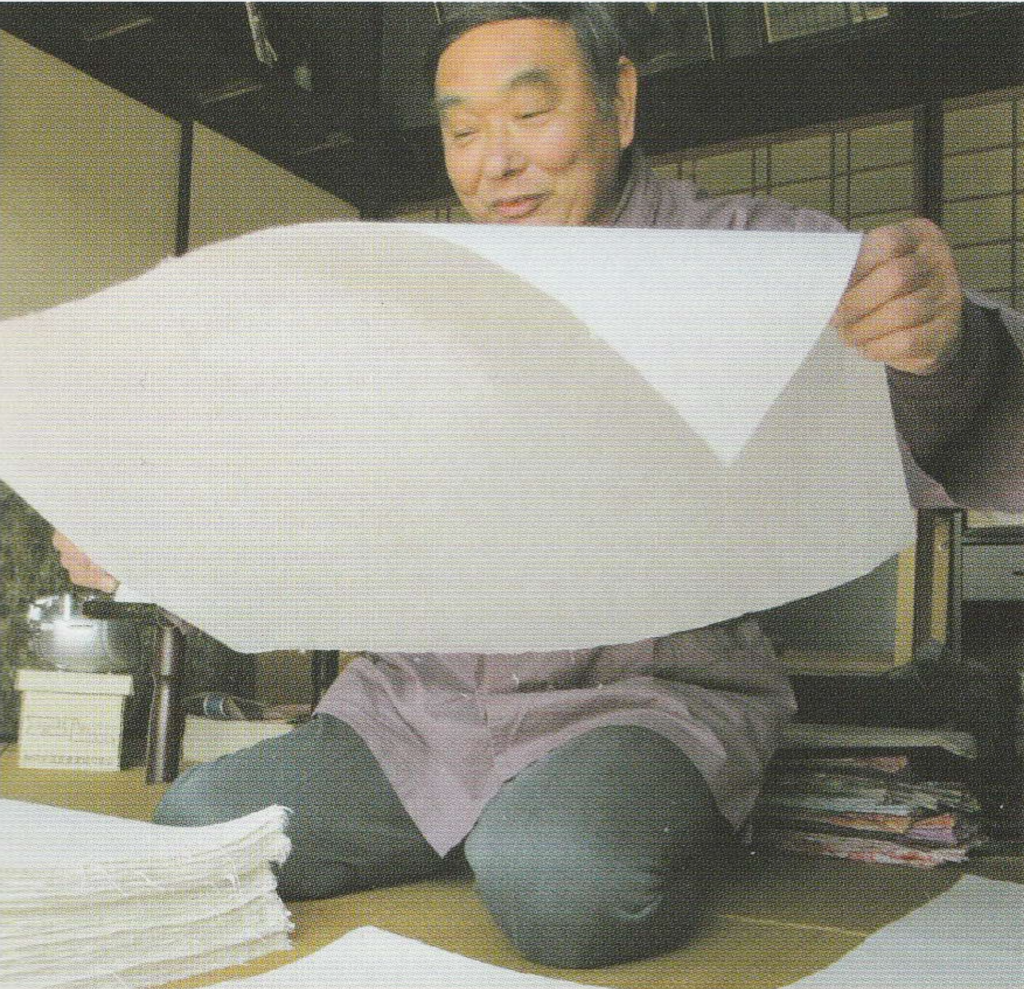
After drying, the paper is taken indoors, examined, and sorted. The highest quality paper, with no visible blemishes, is given a rating of 1. Paper that is found to have even the slightest imperfection is given a rating of 2. Each sheet is examined with great care.
【Illustrations of Paper making processes】








